A visit to the B&O Factory
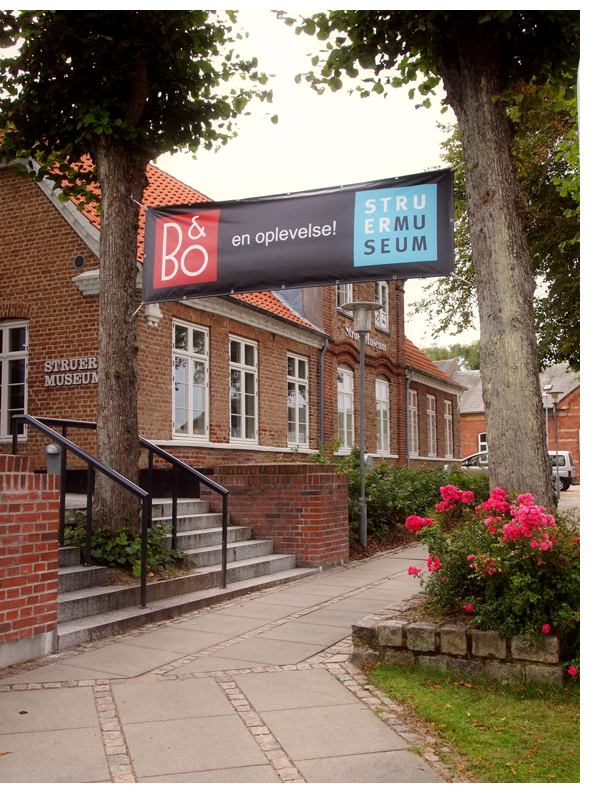
The look and feel of Bang & Olufsen products tells only part of the story. A trip to the B&O factory in Struer, Denmark, tells the rest. The hardwood floors that I encountered at the Copenhagen airport underscored the ethos of style and design that permeates the Danish culture. B&O’s corporate headquarters looks more like a museum of contemporary art, or at least a very cool furniture store, than a factory where HiFi gear is produced. But it wasn’t always that way ...
Peter Bang and Svend Olufsen started B&O in 1925. College friends, Olufsen was the marketing half of the company and Bang was the engineer. The manufacturing facility began in an unused part of the Olufsen home and farm. Their first product was called “The Eliminator” because back then, radios ran from lead-acid batteries that emitted harmful fumes in the home, and no one thought it would be possible to power a radio from the AC mains. The Eliminator showed they were wrong by ditching the batteries for AC current.
Today, Bang & Olufsen is a major employer in Denmark and there is a museum in the center of Struer that documents every step of their achievements. If you love HiFi and find yourself in Denmark, a visit to the museum is a must. They have an original Eliminator there as well as every other product that B&O has produced over the years, right up to the current day.
It’s fascinating to see how their product mix evolved. For years, they made microphones, movie projectors, even electric shavers! But from the 70’s on, they stuck to their core technologies, concentrating on HiFi systems and televisions, and lately automotive HiFi systems. In Issue 22, we reviewed the B&O sound system in the current Aston Martin DBS; B&O produces the premium sound system in the full line of Audi cars. I saw a few parts on the factory tour that suggested that they may be producing sound systems for a few other automobiles in the future, but we shall see.
You might be surprised at how traditional some of their products looked at first, but it didn’t take B&O long to develop their distinctive style. I believe this began in earnest in 1939 with the BeoLit 39 radio, which featured a case made entirely of Bakelite. A somewhat brittle plastic, it was a relatively new material at the time and was deemed tough to mold into complex shapes. But B&O’s designers pushed for Bakelite, and the engineering staff devised a process. This design-driven way of doing things at B&O continues to this day.
As we were told by our host at B&O, Jette Nygarrd, “The designers are given free reign here. It is our job to turn their vision into current products.” It is worth noting that the designers at B&O are not company employees but contract workers. The company feels this allows them the autonomy to challenge their vision, which might not be as free if they were worried about pensions and stock options.
Style, performance and precision
B&O puts an equally high priority on the performance of their products and rigorous quality control. While many audiophiles are curious about sonic testing and specs, B&O takes it way beyond that. They had numerous labs to measure every electrical parameter possible and two listening rooms where the speakers are hidden behind a transparent screen.
They employ about a dozen people who are their “Golden Ears,” trained strictly to listen to nuances in prototypes and final products in a real environment. These test listeners are asked to make notes and comment on every aspect of the sound on a wide variety of program material. Although in our demonstrations, we had to listen to The Eagles’ “Hotel California” a little more than I cared to!
On a parallel track to what’s going on in the engineering department, there is another department that is trying to destroy their creations. This is what gives B&O such a high reliability rate. A worker at one workstation is simulating high vibration, while another repeatedly drops a television set from 10 feet in the air. Yet another machine pushes buttons in and out, while others bathe their products in heat, cold and humid conditions. They even have a machine that blows cigarette smoke into the air, which is equivalent to one of their components being exposed to a one-pack-per-day smoker for 10 years. Remote controls are bathed in the equivalent of human sweat to see how long it takes to wear the markings off them.
One of the engineers told us an interesting story about a man who was complaining about how his remote control had become discolored and the markings had faded prematurely. The B&O engineers finally figured out that cancer medication he was taking had changed the pH balance of his sweat, and that was something they hadn’t planned on. I came away convinced that there is no torture to which B&O products have not been subjected!
We also got to see a full, working example of a B&O store. This is where a lot of corporate training is done, and it helped us to get a feel for how B&O works with their customers, as well as seeing all of the latest products. Unlike other HiFi companies that work through a dealer channel, B&O takes the Apple store route and has all company-branded stores.
We ended our trip with a demonstration of B&O’s spellbinding 103-inch plasma TV that should be in stores right after the New Year. The demo room was very sparse with four BeoLab 5 speakers at the far corners. Although a $140,000 plasma isn’t for everyone, it again underscored the fact that B&O has the technological capabilities to deliver cutting-edge products.
While Bang & Olufsen is occasionally criticized in the audio press for putting style ahead of substance, nothing could be further from reality. After spending a few days at their factory, it is obvious that while aesthetic appeal is very important, their commitment to technology, engineering and vigorous testing is unmatched in the industry. Granted, the Danes like to do things their way, but that’s what gives their products soul. For my money, we could all use a little more style in our everyday lives.